The holy grail for total joint sales representatives is to place vendor-owned instrumentation on consignment at a hospital or ambulatory surgery center (ASC). This opportunity greatly reduces the day-to-day logistics demand on the representative and the local sales organization and creates more selling time. Cases at the facility can be prepped by simply resetting the existing instrument inventory. The surgical facility provides the storage for the sterilized units for an indefinite time between uses.
Why is this consignment strategy beginning to strain in the presence of several new factors in the market?
1. Increased sites of care for the procedures.
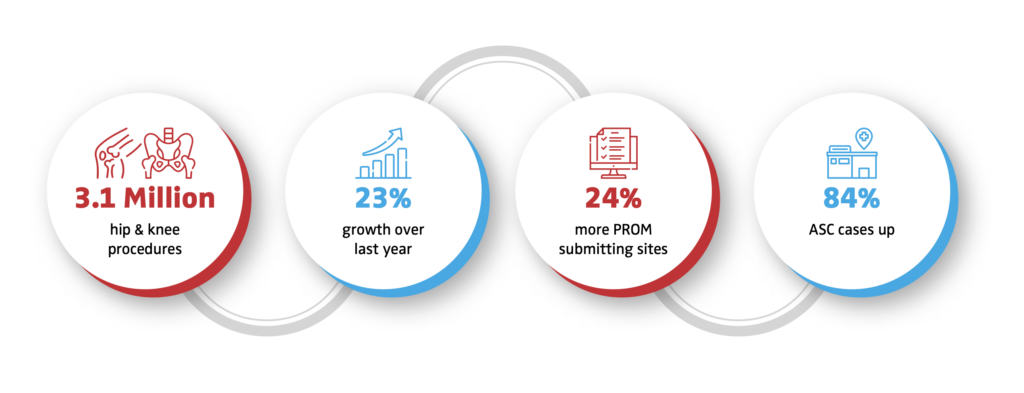
AAOS American Joint Replacement Registry 2023 Annual Report
2. Individual physicians working at multiple sites of care.
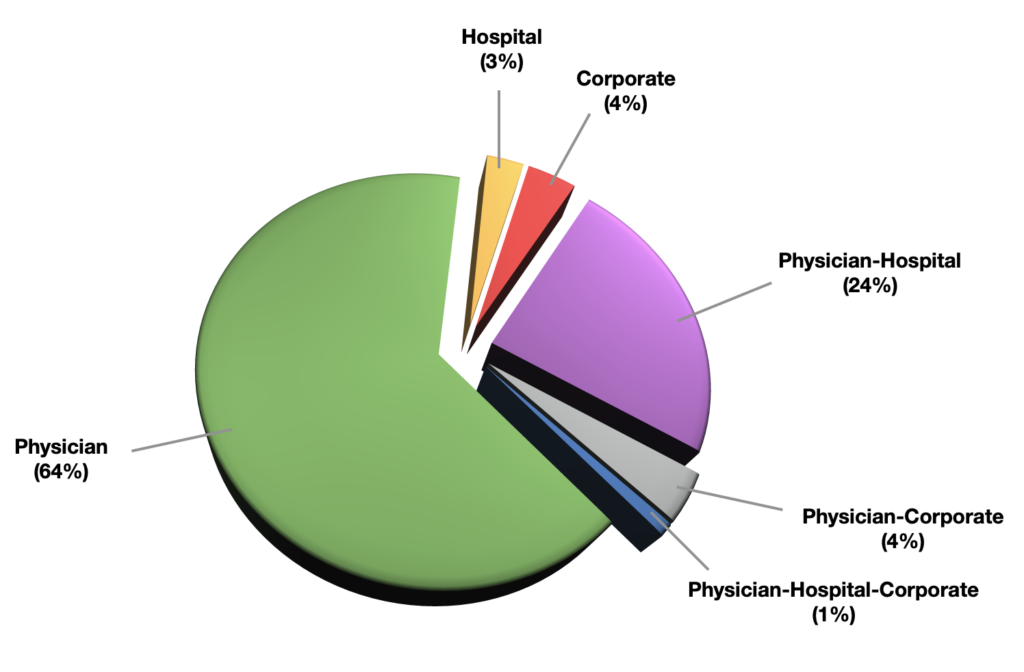
Physician ownership in ASCs makes up the majority. ASCA’s 2017 Salary & Benefits Survey.
3. Patients are choosing ASCs for convenience and lower costs.
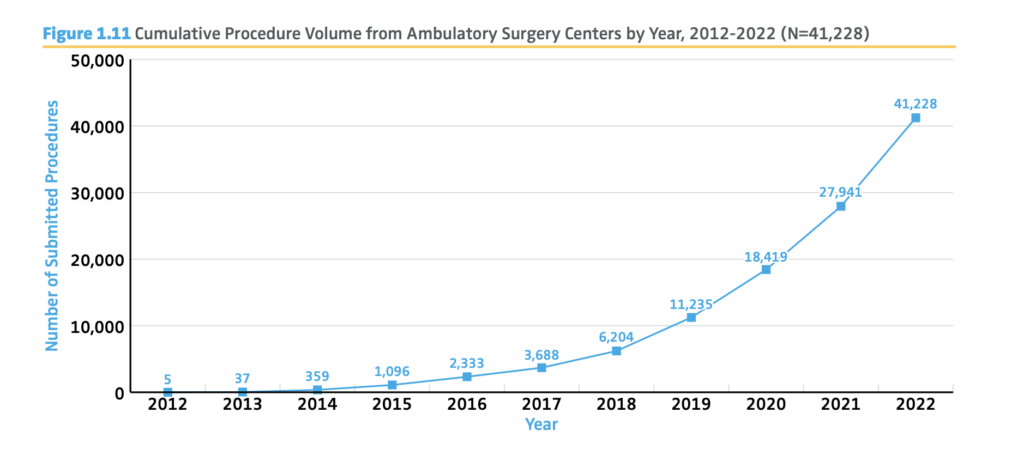
AAOS American Joint Replacement Registry 2023 Annual Report
4. Greater lead time requirements for deliveries at ASCs.
“To allow adequate time for quality processing, the instrumentation should arrive in the decontamination area at least 2 working days (48 hours) before the scheduled surgery for existing loaned sets, and 3 working days (72 hours) for new sets, which will require training for both SPD and OR staff.”
Susan Klacik, BS, CRCST, ACE, CHL, ACE, FCS,
OR Manager October 21, 2020
https://www.ormanager.com/timely-delivery-needed-ensure-safety-loaned-instruments/
5. Increasing total joint volumes.
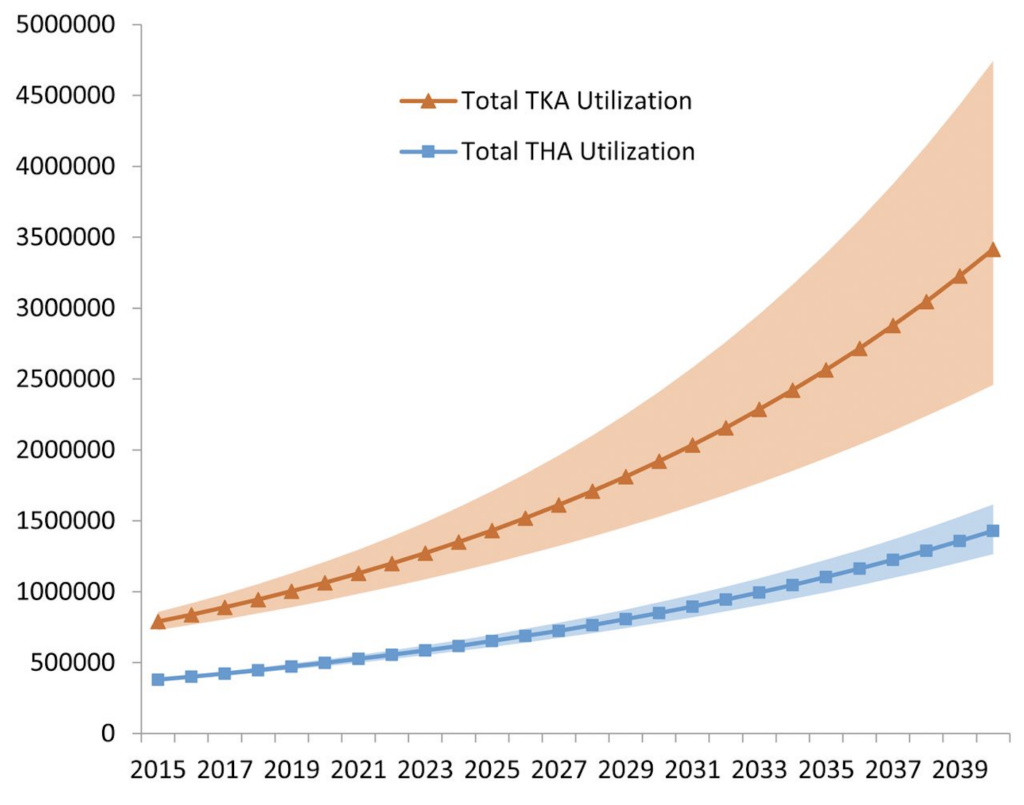
The Journal of Rheumatology September 2019, 46 (9) 1134-1140; DOI: https:// doi.org/10.3899/jrheum.170990
The additional points of care are straining the classic facility consignment model. Instruments will increasingly be underutilized when consigned to a single surgical facility in the future due to the factors above. Additionally, these new sites of care, specifically ASCs, have limited decontamination, sterilization, and storage capabilities compared to the typical hospital.
The reality of these cumulative and compounding factors is that the industry must adopt a more sophisticated service profile to meet the needs of the surgical facilities and ultimately the patients receiving these devices. We believe a consolidated “3PL approach” will be the next logical advance that will bring value and higher margin to all.
Enter the Sterile Processing Logistics Center (SPLC)
A Sterile Processing Logistics Center (SPLC) will provide the sophisticated logistics and processing needed to create efficiency in the supply chain relationships between surgical facilities, total joint manufacturers, and the patients receiving these devices.
Centralizing the available instrument inventory in a market and creating time savings by delivering the instruments sterile to the surgical facility will provide the most efficient use of the instrumentation for all. Surgical facilities would no longer need to process and store the instrumentation in either a consignment picture or manage the decontamination and sterile processing of the equipment delivered on a per case basis.
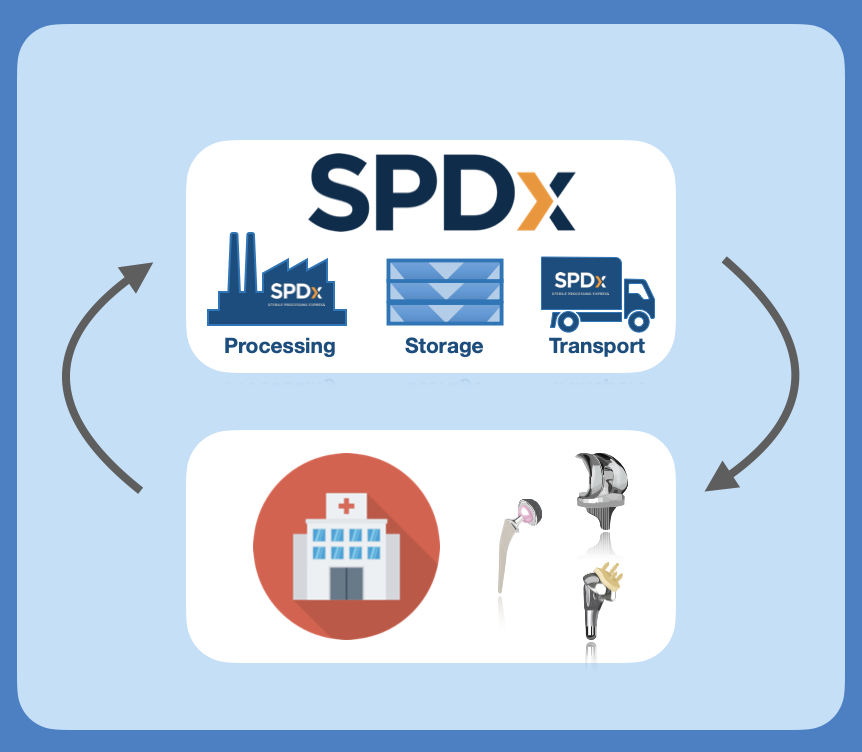
Sterile Processing Logistics Center
SPLC Standards
SPLCs will need to operate on a set of standards aimed at replicating and exceeding the processes managed in the traditional sterile processing departments at hospitals and surgery centers. These new facilities will need the following to manage these aspects of patient care:
1. Robust Quality Management Systems.
The guidance provided by the total joint manufacturers must be followed strictly to ensure that all aspects of the IFU are properly executed. This means that all of the equipment required, the time on station needed, and the training of the personnel are available at the SPLC and are well monitored by the management team. A formal quality management system, along with seasoned clinical leadership guiding the execution, will provide excellent patient care.
2. Certified Sterile Processing Technicians
The breadth of knowledge needed to properly service a variety of surgical instrumentation in decontamination, sterilization, storage and transportation is massive. The very best resource available to execute the daily activities are certified sterile processing technicians intimately familiar with all of the techniques, best practices, and regulations that guide these departments.
3. Purpose Built SPLC Facilities
Purposely designed facilities will provide the efficiencies needed to create value for the instrument manufacturers and the surgical facilities. These facilities can take a factory design and approach the processing in a way that normal departments located at the surgical facilities will never accomplish, given their natural constraints for space.
4. Dedicated Transportation
The guidance provided by ST79 regarding the transportation of sterile equipment is all centered around controlling the environment during transportation. The capability of the vehicles needed to maintain this environment will be different in the varying geographies, but must be able to perform this vital environmental function. Additionally, there are requirements for cleaning and disinfection that will be best served by facilities owning, operating, and maintaining their own transportation elements.
5. Customized Software
Software is the key to all of the tracking, documentation, planning, and analysis that will be needed in these facilities. Surgical facilities will need access to sterilization records, chain of custody records, environmental documentation from the building and transportation.
Total joint manufacturers will want the chain of custody, turn rate information and maintenance records for the instrumentation they provide for surgeries serviced by the SPLC.
The facility itself will need a large database of easily accessible IFU, regulatory, and other processing information on a daily basis. Combining all of these elements will require customized software that services all of the participants.
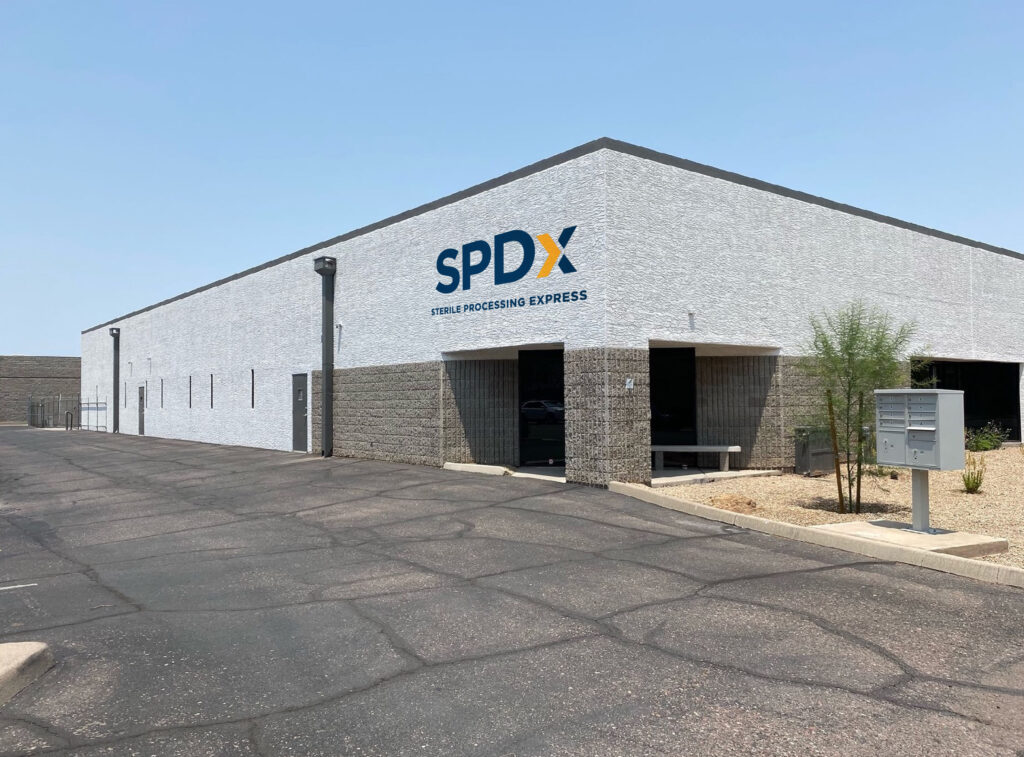
Independent SPLCs will be a revolution in healthcare logistics. These facilities will be well positioned to provide value to both the surgical facilities and the total joint manufacturers as our population in the US continues to seek elective surgical care in more convenient and cost-effective venues such as ASCs. The SLPC facilities will also provide a valuable resource in their communities by providing sterile processing capacity backup in emergency situations as well as planned downtime at the existing surgical facilities for maintenance and facility improvements.
Sterile Processing Express, LLC has opened its first of many SPLCs planned for the United States in Phoenix, AZ. The Phoenix facility is operational and will be servicing the surgical facilities in Phoenix and Tucson.
Please direct inquiries for services and investment opportunities to: