The Journey from 20 to 60 Total Joints per Month in an ASC
Authored by Dick Winiker, in collaboration with Banner Surgery Center – Gateway
Case Study
The opportunities to serve more patients in the ambulatory surgery center (ASC) setting are growing by the day. The drivers for these opportunities are the patient preferences, the new surgical technology available and the costs savings unique to the ASC setting. There will be many new ideas that fuel the growth of procedures in the ASC setting and below is one facility’s experience with a developing healthcare outsourcing segment known as off-site sterile processing.
The National ASC Opportunity in Total Joint Surgery
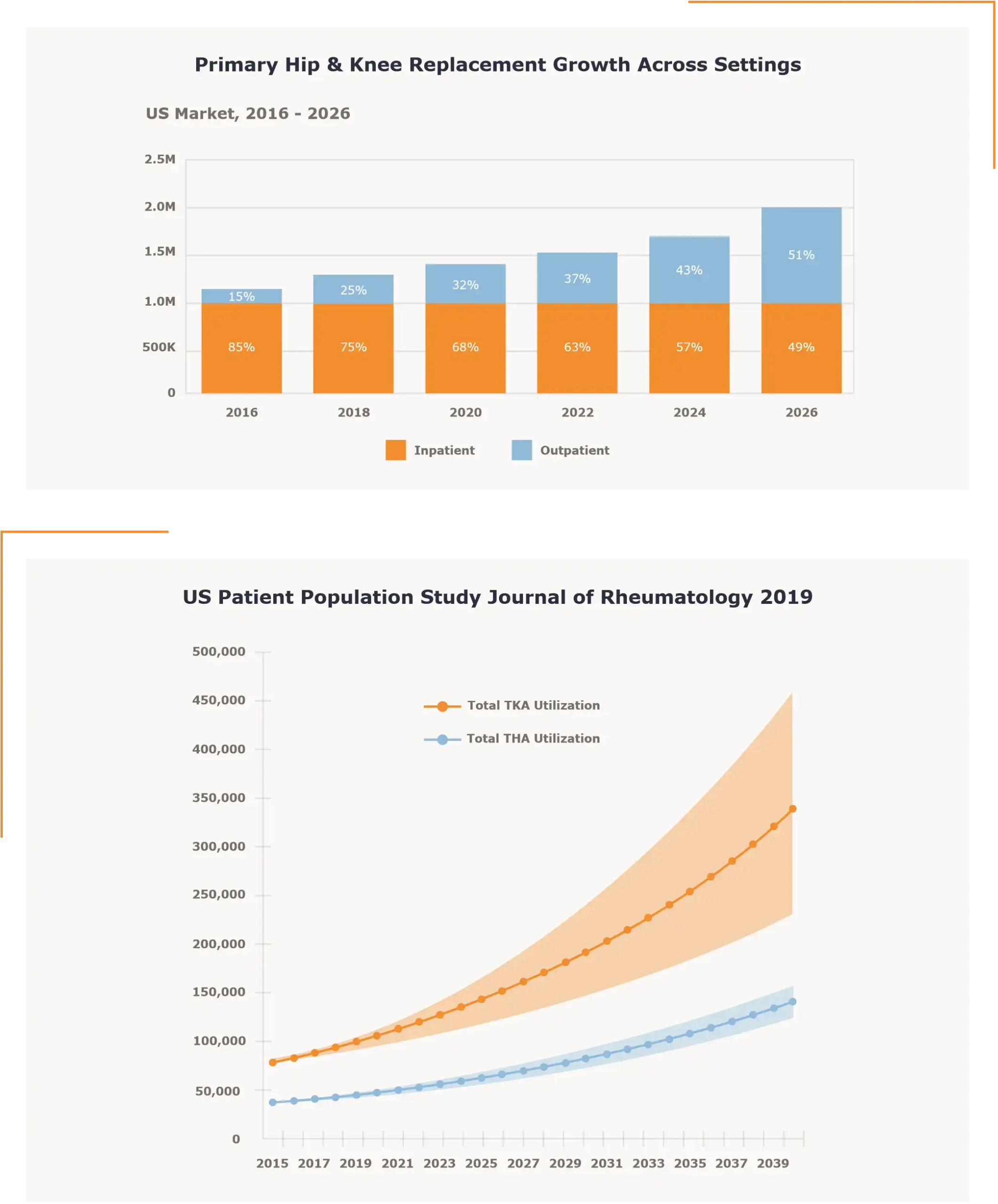
Case Study
Banner Surgery Center – Gateway Orthopedics (BSC) is a seven operating room orthopedic surgery center in Phoenix, Arizona built in 2004. The current ownership is a combination of a hospital based corporate partner and individual physician ownership.
BSC has physician partners that can provide total joint volume to the facility with patients that are well qualified to be treated in the ambulatory setting. The challenge for the facility like many others in the US is a lack of capacity in both the SPD department and the needed storage areas. Many facilities across the country, like BSC, were not built with a total joint service line in mind, and the SPD capacity needed for those cases. This is an opportunity and accompanying challenge that almost all orthopedic based ASCs are facing daily.
BSC and their ownership partner set about exploring the opportunity to increase the total joint service line in the facility. This endeavor led to a number of questions:
Is there an opportunity to increase the Total Joint service line in the facility?
The ownership group managing BSC included the physician owners and the management partner Atlas Healthcare Partners based out of Phoenix, AZ. This group along with the physician ownership group and the onsite facility management formulated a target for total joint surgery volume. This volume was based on the referral opportunity, patient population available in the area, available OR time, along with the capital investments in instrumentation that would be needed at BSC. The target was set at 60 to 80 total joints per month. Once the target was set, the questions surrounding the internal SPD and storage capacity began to develop. How would the facility manage the greater throughput and storage of the trays required for a dramatic increase in the total joint service line?
What volume of Total Joint surgery can be performed with the existing SPD infra-structure and storage capacity in the facility?
A time study using real surgery schedule data broken out by CPT code was used to create a throughput model for the SPD department. The data provided was for the entire surgery schedule for three months with all service lines. The preference cards for the procedures were used to identify the sterilized trays that would be needed for each case and the estimates including all vendor trays that would be requested as well as the facility owned trays needed to complete the various procedures. The facility would do 350 to 400 surgical cases in the months that were sampled. In those three months, there was an average of 20 total joint cases performed in the facility.
Station times were built into an Excel model using the unique manufacturer recommendations for each tray as they moved through the decontamination and sterilization processes at BSC.* Vendor trays were assumed to be brought in per case required in the model. The significance of that assumption in the model is that a decontamination cycle is required on the arrival and on the departure of those trays. This is a fairly common process in an ASC and many hospitals as well. Also, the facility had very few unused storage spaces. The opportunity to consign for sterile storage or hold the trays at the facility in an unsterile status until needed were limited. The data suggested that BSC could do 20-25 units of total joint surgery in a month and maintain the flow through the SPD department while managing the throughput of trays from the other service lines such as hand and sports medicine. The one exception to that situation was when the total joint case were going on back to back days. In those instances, the decontamination area and staff would become overwhelmed with trays coming into the facility for a scheduled cases and trays that needed to be decontaminated to leave the building from the current day’s schedule.
*Note that the study SPDx performed also assumed best case scenario for vendor performance. In our model we assumed that all trays were delivered and retrieved on time by the vendors servicing the facility.
Could a rebuild of the SPD department work?
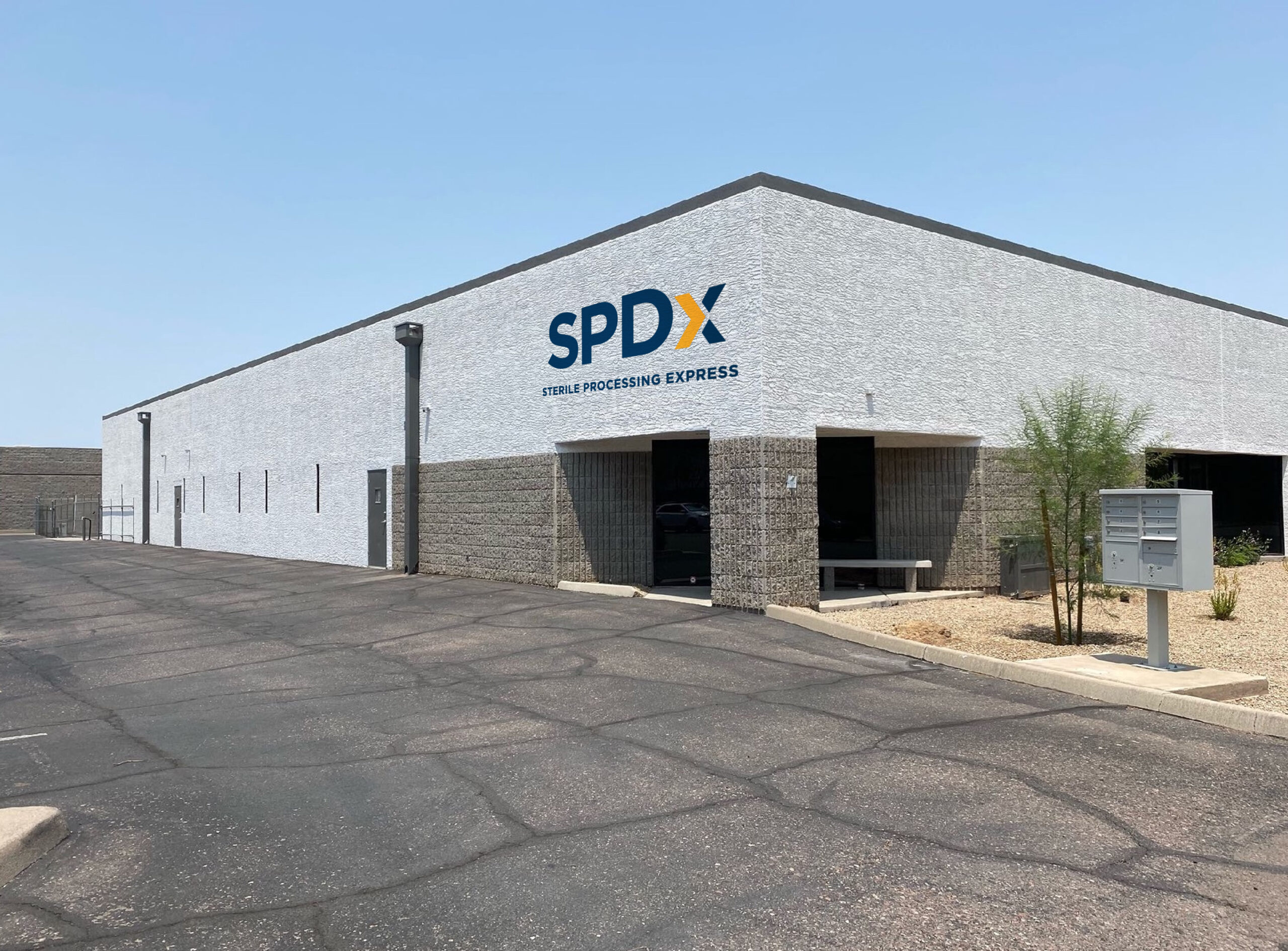
Like many surgery centers built some years ago and well before CMS allowed total joint hips and knees in the ASC setting, the facility was built to manage sports medicine, hand surgery and small bone fractures. The center functioned well with the designed capacities of storage and SPD capacities for many years and was able to handle a small volume of total joints. As the total joints began to arrive, first with the private payer patients and then with the CMS addition of total knees in 2019, total hips in 2021 and finally total shoulders in 2024 the facility needed to consider the upgrade of both SPD capacity and storage capability to serve the volume available in those service lines. Estimates for that type of revision to the SPD department were upwards of $2,000,000. The facility would have to capture additional space for the new configuration by taking storage areas and a common hallway that is used to access the current department. While the new department could be envisioned, the reality of increased volume means an increased need for storage capacity for both sterile and non-sterile vendor trays. Additionally, there would need to be an increased storage requirement for facility owned trays to support the additional total joint case volume. There are usually four to five facility owned trays that are used in total joint procedures. Another factor to consider is that at higher volumes of total joint surgery vendor performance becomes critical. Any challenges to the timing of the vendor driven logistics create problems in SPD production needed to prepare the sets for surgery and a variety of storage problems for the surgery center. At the same time all of these assessments were being tabulated and considered, a new off-site sterilization company with a facility in Phoenix Arizona came on line. Now an alternative to the standard in house SPD process existed for BSC and the entire Phoenix metro area. The company is Sterile Processing Express, or SPDx.
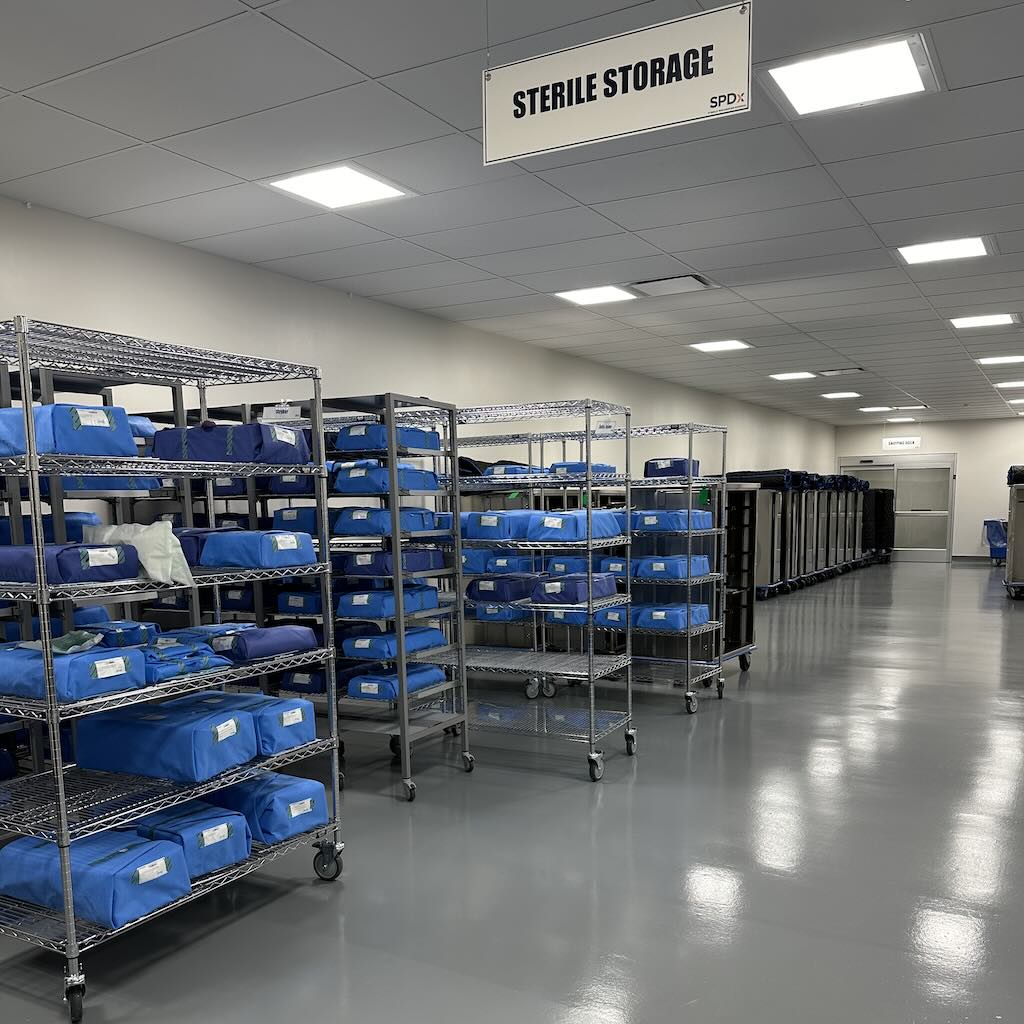
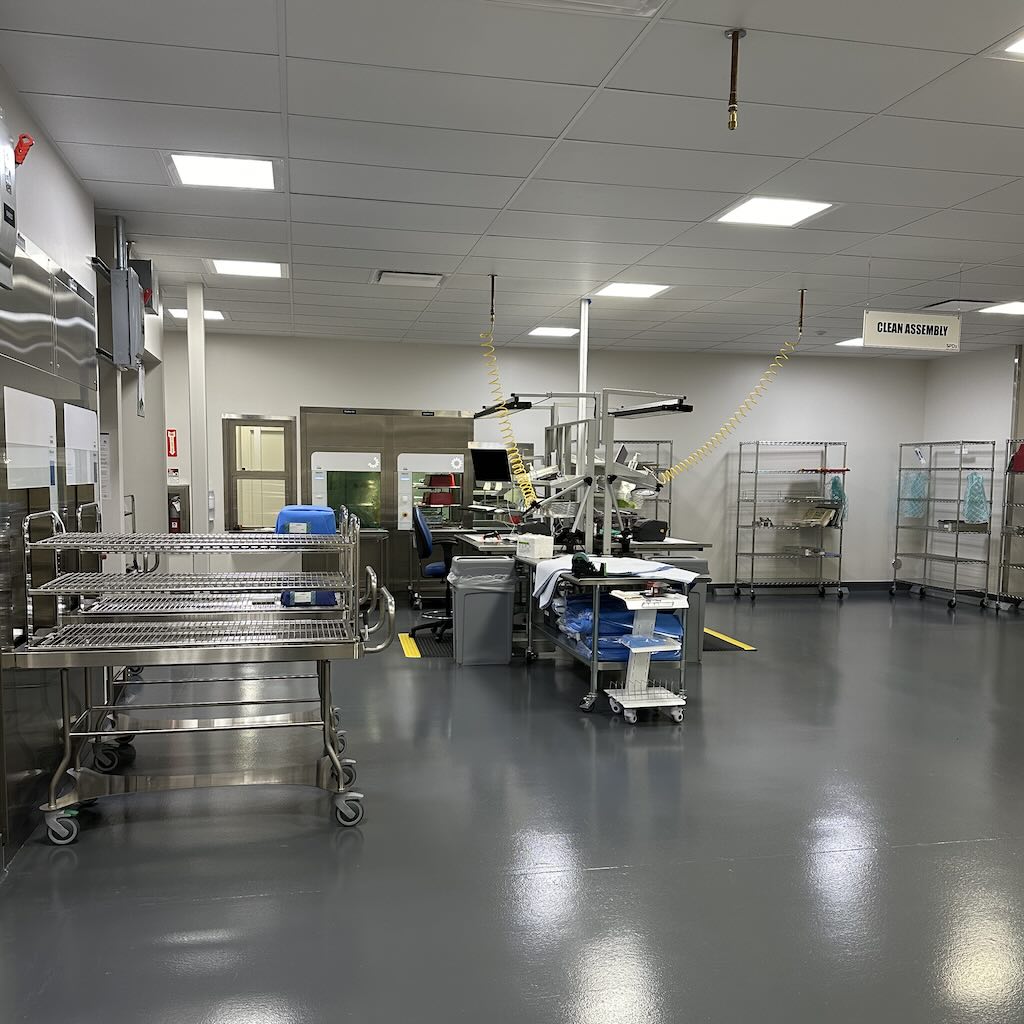
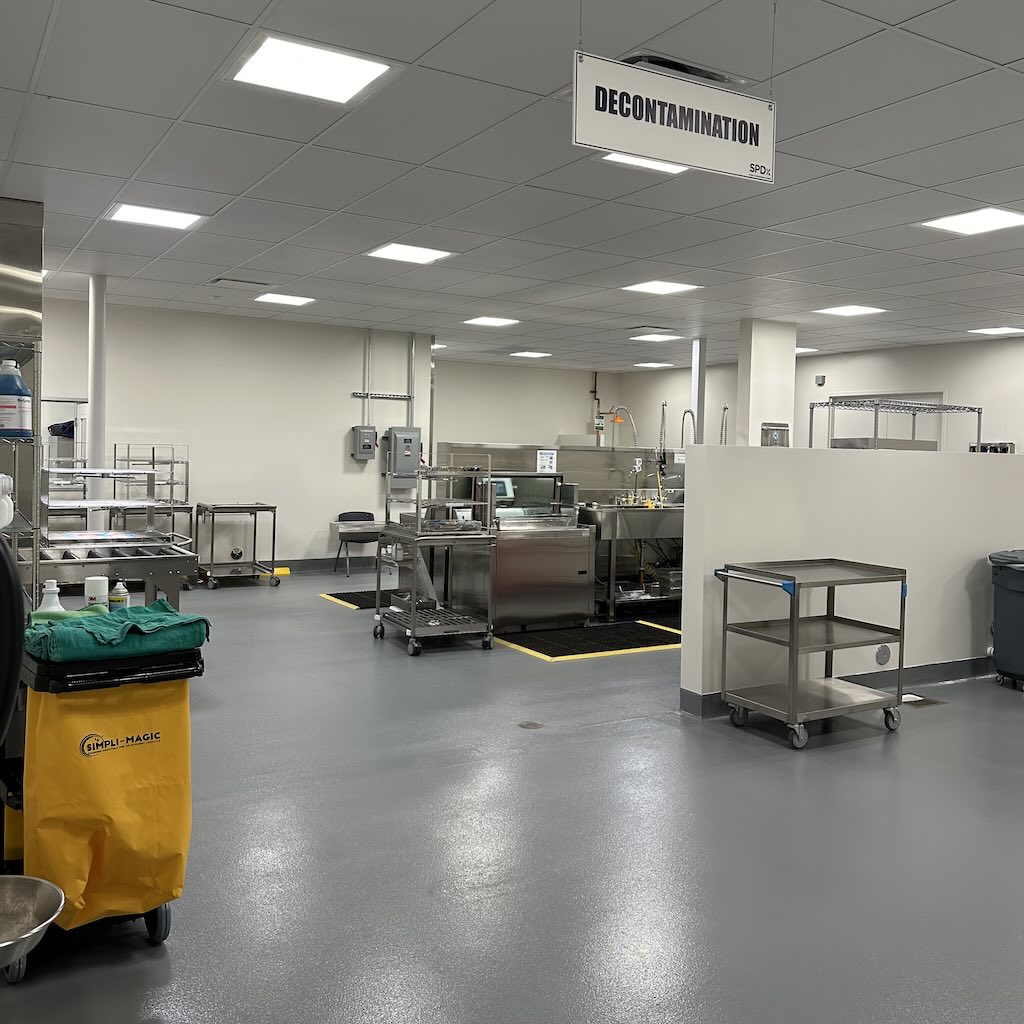
This alternate opportunity created a number of questions. The first question to be answered was:
Is there an opportunity to increase the Total Joint service line in the facility using an outside sterilization service?
The use of an outside SPD processor in this environment is somewhat different than the classic models that have existed for more than 15 years in the United States. The typical situation is a large university based healthcare system or a large IDN will build a facility to support their existing facilities and service all of the instrumentation used. SPDx in Phoenix was built to manage the logistic movement and sterile processing for vendor owned total joint trays. The facility can also support facilities in need of general instrument processing, but the building design and equipment installed were optimized for the unique efficiency needs related to total joint tray processing and movements. SPDx in Phoenix was well positioned to support added total joint case volume at BSC.
Can the off-site sterilization service be used within the existing regulations?
Off-site sterilization facilities have been active in the United States successfully for more than 15 years. As mentioned above, most of these facilities have been associated with University health networks or large IDNs. Recently, there have been a number of start up businesses looking to address the capacity and logistic needs of surgical facilities from a third party supplier position. All of the regulations related to the operations and standards of these entities are written in the AAMI ST:79 sections related to transportation of sterilized equipment and contaminated items.
Can the outside service be compliant with the current facility policy structures?
Current policy in most facilities, including BSC, do not allow items sterilized at other facilities to be used in surgery without going through a decontamination and sterilization process on site. This policy exists in most facilities as a reaction to the days when people, mostly vendor representatives, would move a sterilized tray from one facility to another and it would be used without processing at the receiving facility. That practice was challenged with the meeting the proper transportation requirements, the sterilization record keeping and general handling of the tray as described in ST:79. This made the activity risky to the facility electing to use the tray as delivered. BSC would need to re-write the policy to include sterile tray delivery from an dedicated off-site sterilization facility and include the details that would describe the nature of the facility they would consider to be appropriate for such activities.
Sample Policy:
Loaner equipment received as packaged or ridged containers from another healthcare facility are deemed unsterile and must be disassembled, decontaminated and re-sterilized according to the manufacturer IFU associated with those items. The exception to this policy are items shipped sterilized from a purpose built facility that specializes in vendor tray sterilization and is transported in a climate controlled vehicle meeting all of the ST:79 parameters. Such facilities must have a third party survey such as DNV, or Joint commission and must be ISO 9001 compliant.
Could the outside service meet the sophisticated IFU requirements that are associated with these types of trays?
The SPDx facility was designed with strict attention to the IFU requirements for each instrument and tray from the manufacturer. AORN guidance and Joint Commission are very clear about the requirement. Initial rinse, soak times, ultra-sound cycles, mechanical washer settings and every other element of any individual IFU are managed daily in the facility. To assess the capability at SPDx, BSC and the managing partner, Atlas Healthcare Partners, launched thorough evaluation of the off-site facility in Phoenix. This evaluation included elements of a mock JCAHO survey to observe the processes and personnel in the SPDx facility. Every aspect of the SPDx operation was juxtaposed against the in house BSC/Atlas requirements to assure that all areas of the operation were in line with the normal process and documentation requirements in place at the surgical facility. With one minor adjustment to add patient chart labels to the packaging, the systems were aligned.
Can the outside service provide the chain of custody and processing records needed when requested?
Off-site sterilization facilities have been active in the United States successfully for more than 15 years. As mentioned above, most of these facilities have been associated with University health networks or large IDNs. Recently, there have been a number of start up businesses looking to address the capacity and logistic needs of surgical facilities from a third party supplier position. All of the regulations related to the operations and standards of these entities are written in the AAMI ST:79 sections related to transportation of sterilized equipment and contaminated items.
Can the outside service be compliant with the current facility policy structures?
One aspect of an off-site operation that is critical to the facilities that it serves is record keeping. Just as a surgical facility is required to keep all records needed to document the trays and sterilization processes used on those tray, so must SPDx and they must be made available on request to BSC. The vendor tray processing environment is much more dynamic than managing the information that is created by processing in house trays for a single facility. Also, the ability to retrieve that information and distribute it as requested by a surgical facility that is being served in this manner is more challenging. SPDx has developed a unique way of cataloging and cross referencing the sterilization log information and the individual trays that are processed. The information is digitized for easy access based on individual tray information and or sterilization load information. BSC was provided a number of samples of sterilization records and chain of custody elements to demonstrate this capability. SPDx developed a modified industry software and a number of unique processes that allow the retrieval of any log information requested by a facility in minutes and can send the documents digitally as requested.
Will the vendors accept the off-site model?
Just as any surgical facility working with vendor supplied trays, the off-site provider will need to work with the vendors to coordinate the logistic activities. The total joint vendors servicing BSC will need to adapt and embrace the new model. When queried on the subject, most vendors were willing to work with the new system because their logistic operations are straining their systems as an increasing number of facilities are adding total joint service lines. Those that were hesitant were coached along and ultimately embraced the new service and process as a benefit to their operations after the formal operation started.
Can the outside service perform at the level needed to maintain the surgeries scheduled in the facility?
BSC needed to make some assessment of the processing and logistic capacity of the off-site provider. Is there enough personnel? Do they have the equipment needed to process at the needed pace? Is there enough transportation infrastructure such as temp controlled trucks and off-site designed case carts to move the trays outbound sterile, and return in a controlled contaminated state to the SPDx facility? The delivery and pick up plans were evaluated along with the equipment needed to move the trays securely and in compliance with ST:79. Also, storage staging for the sterile instruments at BSC needed to be identified along with a process for moving the carts into position for contaminated retrieval. Ultimately it was easy to see that the basic infrastructure was in place at the SPDx facility and easily scaleable as the number of surgeries grew.
Can an outside service be cost effective?
Outsourcing opportunities in healthcare continue to grow. Surveys of healthcare leaders on the subject indicate that most outsourcing decisions are based on the expertise of the supplier and the cost saving opportunity.
The unique situation that develops when considering the use of an off-site SPD is that the facility department will still be maintained and operated daily. The question then becomes: “Is our surgery center getting the best value from our existing SPD investments when using and off-site vendor in some way?” Put another way, “Are we right sizing the department using an off-site provider?” This type of consideration never existed in the decision to out-source the laundry functions from healthcare facilities for example, and interestingly many of the same performance questions were raised at the time of that transition. The laundry outsourcing decision was a much easier calculation because the entire department and staff would be removed.
Cost per tray sterilized in the healthcare industry has been an elusive number. There are a range of answers available in the peer reviewed literature, but again, it is a range. The calculations would do the normal fixed costs combined with variable costs of the department, but the research is always geared towards an assessment of alternatives that have to do with numbers of instruments in trays, the opportunity to use single use devices and other such ideas. In most facility calculations the department is just considered part of the overhead for the operation as a practical matter and a discrete charge is never assessed to the case cost per surgery directly.
In this case the growth calculation needed to be considered along with the future investments needed for the facility SPD to manage such growth. Also needed were considerations about operating both the current and the larger sized SPD facility in the future. Below are a tables that help quantify the decision.
Ultimately, the off-site solution offered by SPDx and well studied by the innovative ASC operator Atlas Healthcare Partners and their facility ownership proved to be an effective collaboration.
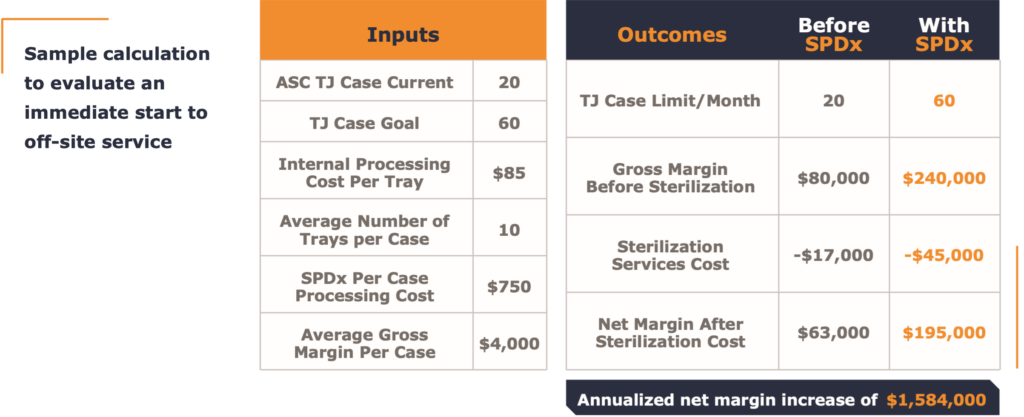
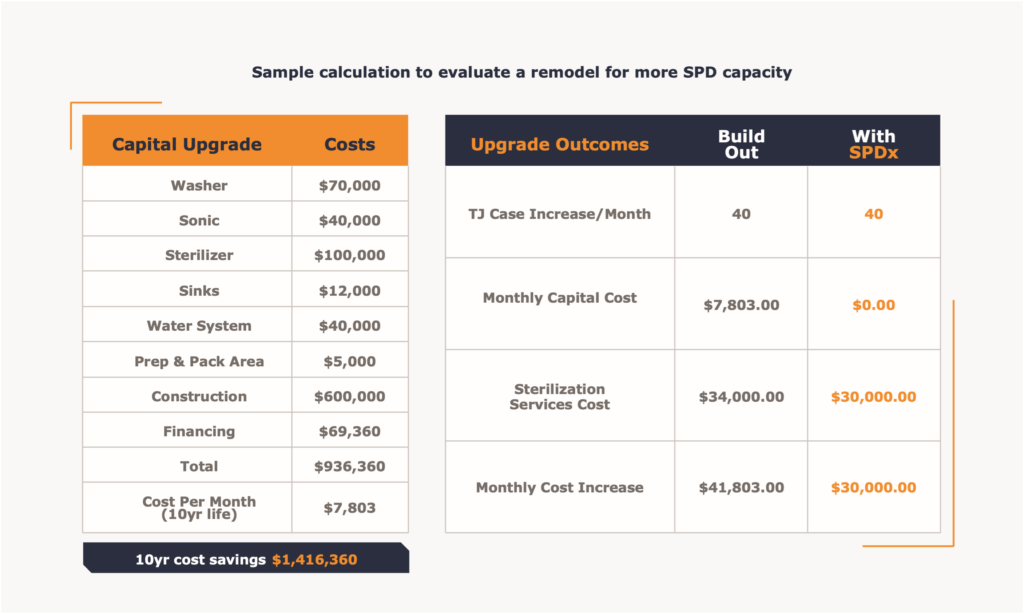
Off-site sterilization will continue to grow in the United States and is well established in University Health Systems and large IDN networks willing to invest in a new opportunity for efficiency. Third party operators will extend this model to many areas. Adoption of the off-site model will lead to entirely new floor plans for new ASCs in the years to come. Existing ASCs will use the off-site model to expand service lines and patient care capacity to patients and providers looking for care in the ambulatory setting. Total joints are but one of the procedures with increased acuity and complexity that will move to the ASC setting as CMS continues to approve more and more procedures available to that setting. All of those procedures will need additional SPD capacity and expertise going forward to make that shift available to patients seeking treatment in the ASC setting.
Hear about the Positive Experience of Jolene Major MS, CEO
“You guys gave us the ability to expand our total joint services beyond what we could do on our own.”
“My recommendation to anyone considering the service is to try it. The amount of daily friction it removes from vendor interactions, staffing challenges and facility capacity constraints is amazing.”
“We will likely upgrade our SPD department when the time comes, but we will keep using SPDx. It is just a better way to manage the total joint vendor trays.”
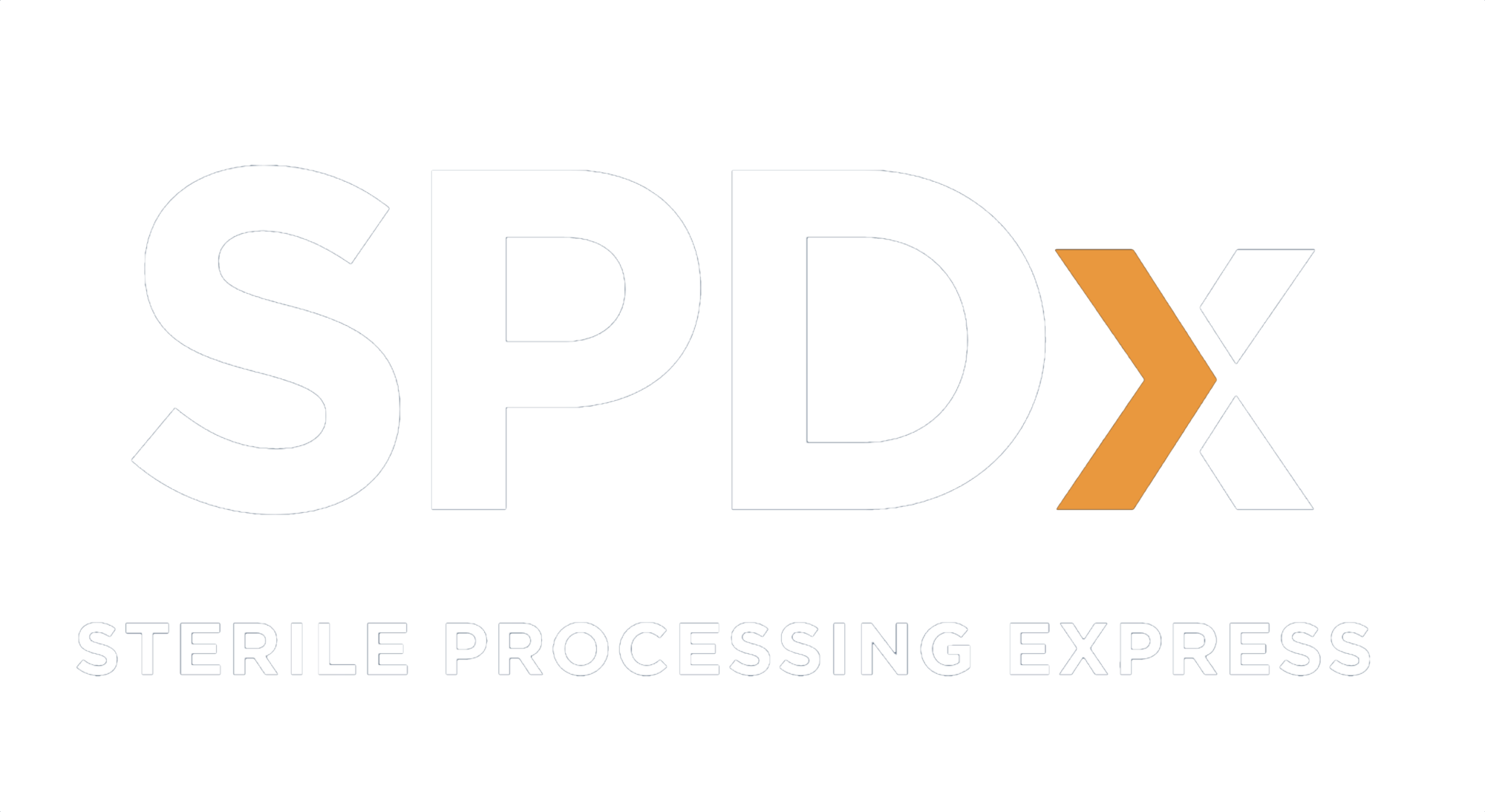
Delivering Patient Care Capacity
© 2024 Sterile Processing Express (SPDx). All rights reserved. This case study and its contents, including all data, graphics, and analysis, are protected under U.S. and international copyright laws. Unauthorized reproduction, distribution, or use of this material, especially for commercial purposes by companies other than SPDx, is strictly prohibited. No part of this publication may be reproduced or used without the prior written permission of SPDx.